General Boat Painting
With a long association with the marine coatings industry, both pleasure and commercial, we have the ability and experience to undertake a wide variety of painting projects. We undertake general boat painting using products such as Awlgrip, Altex Pro- Spray Linear Polyurethane, International Perfection Professional or other quality products either specified by the owner or using our knowledge of products. Our philosophy is to do a good job while giving the customer value for their money. We will not undertake to do jobs where the customer wants to make the boat look pretty enough until its sold, by painting over a substrate that hasn’t been correctly prepared. We highly value our good name and we also don’t consider this fair to the next owner.
When we quote to do a job it will include removing and replacing all the hardware, handrails etc, especially so when the vessel is wooden as these fittings are often a source of leaks or ingress of moisture into the timber or plywood. By checking all these areas before painting any rot or decay will be repaired correctly and then the gear re-sealed down correctly, stopping any further-ingress of water. A cheaper price from someone else who doesn’t remove all the hardware may seem really good at the time but, when one day rot is found caused by leaking fittings, there will be not only a invoice for the repairs but the areas will have to be repainted. Usually rot goes unnoticed until it reaches a critical stage eg the fitting pulls out of the deck.
In some timber/ply/epoxy sheathed boats, repairs will be required to cracking of epoxy sheathing due to water ingress through poorly sealed fastenings in the immediate surrounding areas, or where the sheathing has been sanded thin previously and not repaired prior to painting. In some cases there has been insufficient undercoat film build with the epoxy base undercoat resulting in water ingress, if the sheathing is porous, and in some cases “sand through”, basically covered by the finish coat, either through ignorance or in the quest to do a quick cheap job (cheap for the painter, not for the client in the long run).
All our jobs are spec’d with at least 2 undercoats. Firstly epoxy undercoat as a first stage and secondly urethane undercoat as a finishing undercoat, followed by urethane topcoats. All fairing is coated with epoxy undercoat to ensure it is sealed into the system. This means that every part to be painted will have been sanded at least 3 times and where filling takes place sometimes 5 times. There will be pre-masking for sanding around all the edges prior to any masking for painting. In addition the masking is repaired between undercoats and re-masked prior to topcoating to give clean tidy edges. This is a detail necessary, as, if the edges are not sanded, the coatings may stay there for a while but will start to fall off with time. This is all time consuming and the cost of a quality job .
We own and operate a Valspar tinting system for custom colour stripes and colour matching any repairs carried out by us .
Many people just think “White is just white ” not knowing there are many different shades of white, both produced by paint companies and by people just throwing tinters or paint into white to dream up a colour that looks good to them. A nightmare to eye match. Fade due to UV damage and age is another factor in the equation for the painter when trying to eye match a colour.
Even Gelcoat that has been kept in a tin from when the boat was built will not match the boat once age and UV have taken their toll on the Gelcoat. This is something the owner can find hard to understand when the account has time charged for matching the colour because the original product won’t match.
Painting and repainting alloy and steel boats are another matter altogether.
With steel it has to prepared correctly; sandblasting to remove rust and mill scale is basically the only option ensuring the primer will adhere to the surface pattern created by the blasting. Grinding over steel or rust with a grinder isn’t a solution as all it does is polish the surface to a glass-like surface which nothing likes adhering to! Coating steel is basically a waterproofing process to keep moisture from the steel surface and that’s why it’s important to coat steel to a spec by a paint company, using good quality products.
Alloy is a difficult substrate to paint for a good result in the long term. Many boats, especially trailer boats, have a minimal amount of paint on them, basically cosmetic, applied over a substrate that has in many cases a minimum amount of pre-painting prep carried out.
Marine grade alloy looks after itself quite well in a marine environment, as long as it is washed regularly with fresh water and a salt build-up is kept off it.
Alloy superyachts are successfully painted so as they last but the costs involved are something that in small projects is too expensive to be factored into the project without it being over priced.
Corrosion in alloy boats under a paint system is something that, once it takes hold, can be difficult to remove without major remedial work. It’s something that tends to creep under the coating and, by the time it shows, it’s well underway and eaten into the substrate. Again, people grind out the corrosion and attempt to acid wash it but it’s still in the pits created by the corrision process. Clean alloy can be coarse ground with iron-free fibre discs, giving a pattern for the coating to adhere to. The best option is abrasive blasting with iron-free media such as granite. As a primer the best solution is a chromate based coating to help guard against corrision. In this age of “environmentally friendly” this seems not to be a good option, but it’s a fact of life that it works.
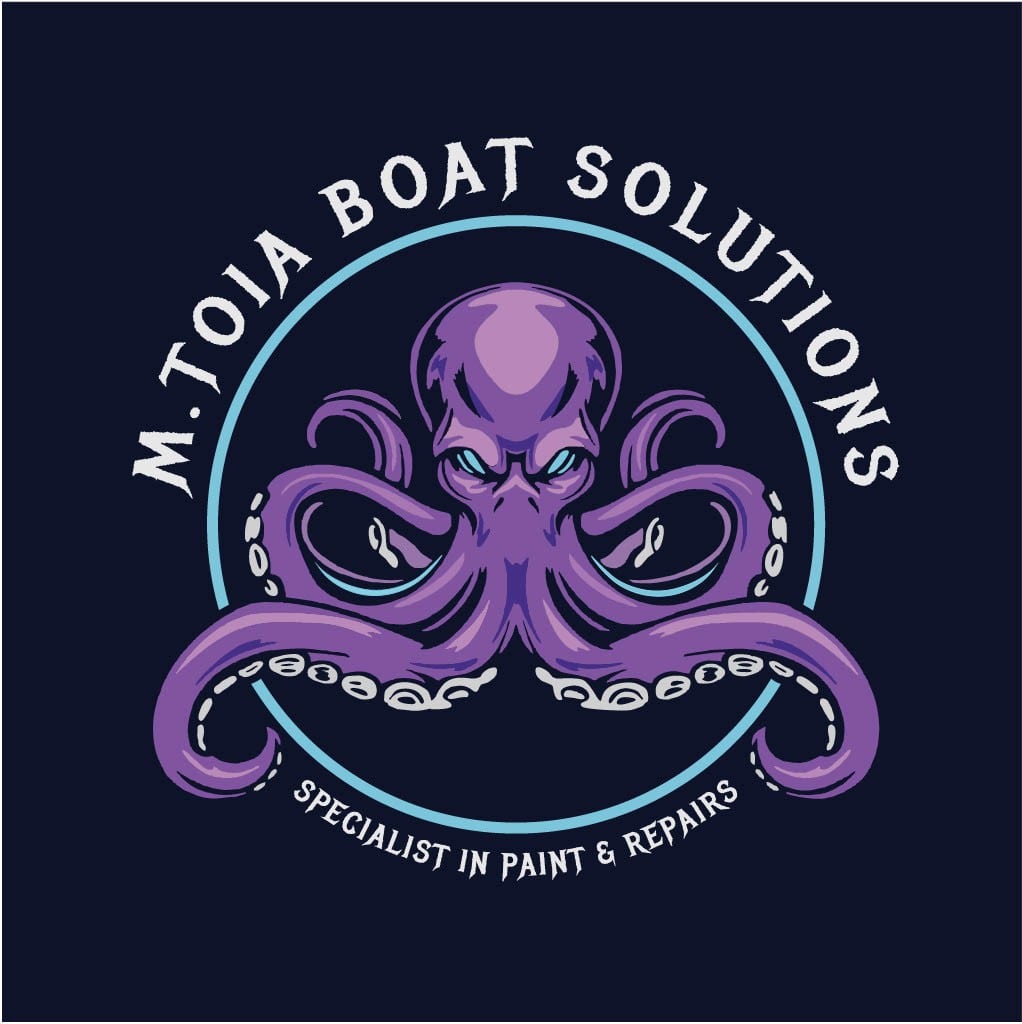
Whitianga Marina Hardstand
WHITIANGA 3510
mtoiaboatsolutions@gmail.com
Mattias PH: 0274 852 031